Roll forming processes can handle ferrous, nonferrous, cold rolled, hot rolled, polished, plated or pre-painted metals. Rolled formed parts are valued for a lot of reasons, among them are uniformity, accuracy, structural integrity and low tooling costs. Read More…
ISO 9001:2008 certified manufacturer specializing in custom roll forming. Unique profiles are run in gauges from 0.005" to 0.165" and widths up to 48" on 35 lines. Adding in-line operations may enhance your product.
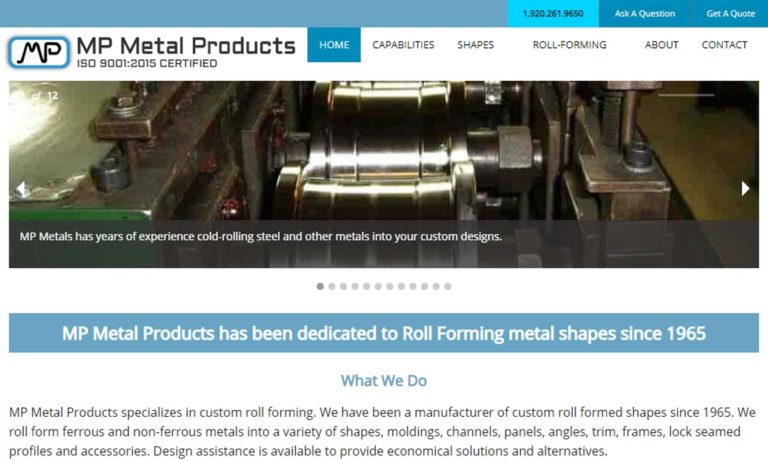
Johnson Bros. is a leading manufacturer when it comes to roll forming metals, pre-finished and plain. Such as profiles, U-Channels, C-Channels, J-Channels, Hat Channels, Box Channels, Zee Channels, Strut Channels, moldings, and more.
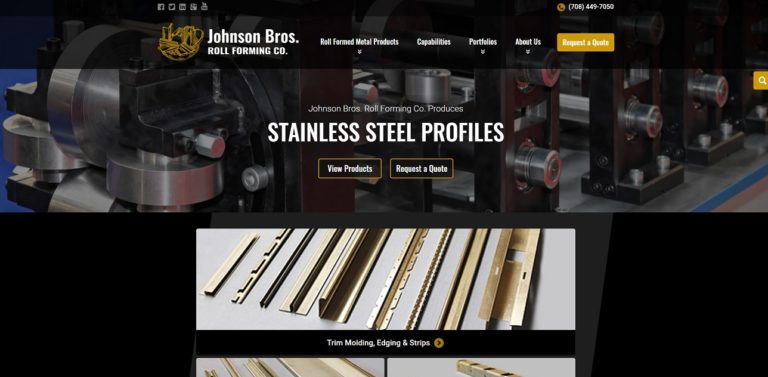
With over 50 years of experience, United Roll Forming specializes in roll forming for a variety of industries. Our products are the result of state-of-the-art machines that provide both quality and efficiency.
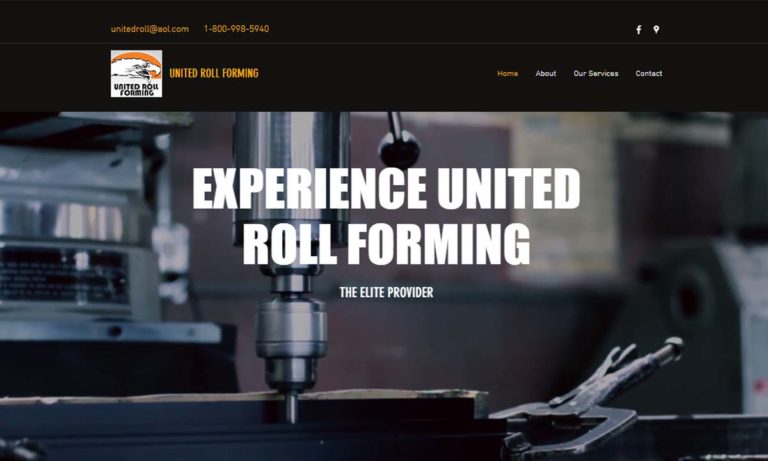
Producing five different standard products, as well as complicated roll forming sections and secondary operations such as notching, punching and fabricating, is Roller Die & Forming Company, Inc. They provide in-house tool room for quality metal moldings and the employees have been trained in every aspect of the roll forming process, representing over 200 years of experience.
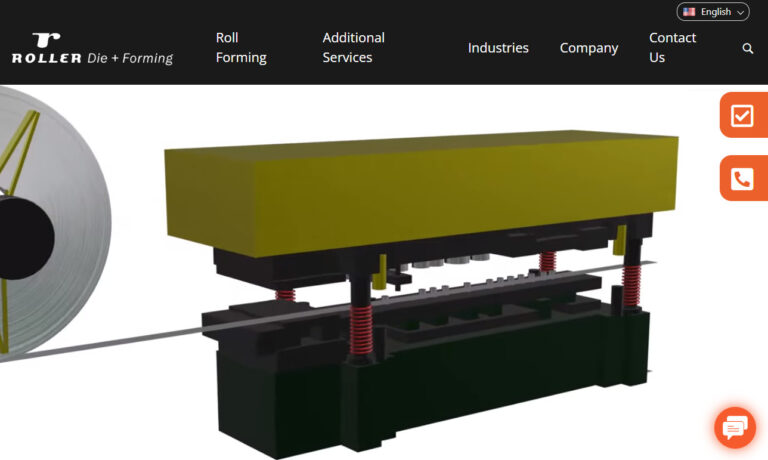
Premier Products of Racine is a full-service company established in 1999 that provides custom roll formed products for applications such as outdoor appliances, tanker trucks, and office furniture. Our 40,000-square-foot facility enables us to perform a variety of additional processes such as custom packaging, welding, and riveting. For more information on what we can do for you, call or visit our ...
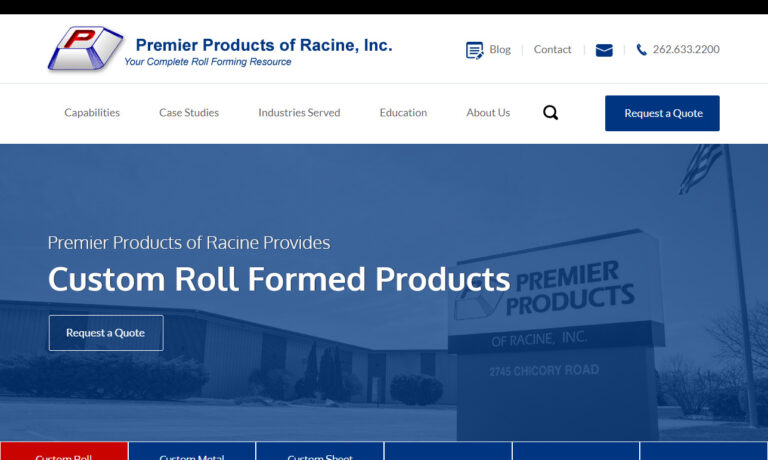
At MMC Roll Form, we specialize in delivering precision-engineered roll formed parts tailored to meet the unique requirements of every project. With over five decades of experience, we’ve built a reputation as trusted partners in the roll forming industry by combining technical expertise with a commitment to personalized service.

More Rolled Formed Part Companies
Rolled formed parts include angle iron, C channels, hat channels, J channels, metal channels, metal rings, metal trim, metal wall panels, steel channels, U channels and more. Industries who use rolled formed parts include aerospace, agriculture, appliance, automotive, building products, elevators, furniture, material handling, railroad, storage, store fixtures and many more.
Since the process of roll forming is easy to repeat, rolled formed parts can be produced at high volumes. A wide array of cross-section profiles can be used in the roll forming process. Open profiles are most common, but a closed tube-like shape can be created also.
Rolled formed steel parts can be produced with either hot or cold rolled forming. Hot rolled steel is rolled at temperatures over 1,000 degrees Fahrenheit. Hot rolled steel is more malleable, which allows it to be forced into a variety of shapes. Hot rolled steel will reconfigure itself during the cooling process, which gives the product looser tolerances than the original material and compared to cold rolled products. Cold rolling processes take place at nearly room temperature. The finished product is strengthened by as much as 20 percent through the use of strain hardening.
Rolled formed parts have found a market niche in the last 10 years or so, with the solar energy industry. Solar panel mounts like fixed ground mounts, tilt ground mounts and roof mounts can all be produced with rolled formed parts. Since the renewable energy market is still evolving and expanding, it is important for manufacturers to contain costs in order to increase market demand. According to the 2016 Solar Market Insight Report, a new megawatt of solar photovoltaic (PV) came on-line every 36 minutes in 2016 and rolled formed parts play a major role in mounting these renewable energy sources.
There are three main factors which impact the cost of rolled formed parts. Complexity of the part, dimensions of the part and volume of the order. Complex parts must pass through the roll former more than less complex parts. More complex parts can take hours to set up the rolling machine and require more tooling, which impacts the costs. Dimensions will affect the cost, though dimensions are less of a limiting factor for roll forming than for brake forming, which is restricted by the width of the press brake. Choosing to construct racking systems from steel instead of aluminum can save up to 30% on cost. Steel may not have the corrosion resistance as aluminum does, but the cost savings have companies opting for steel rolled formed parts.