Rolled formed parts are metal products shaped by a series of rollers, during the process known as roll forming. Roll forming is popular for the production of products in a wide range of industries, including: building construction and architecture, carpentry, commercial automotive and home improvement. Read More…
ISO 9001:2008 certified manufacturer specializing in custom roll forming. Unique profiles are run in gauges from 0.005" to 0.165" and widths up to 48" on 35 lines. Adding in-line operations may enhance your product.
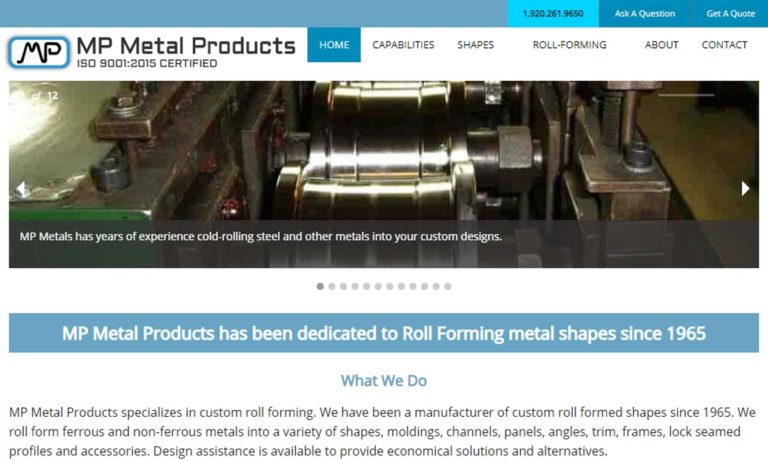
Johnson Bros. is a leading manufacturer when it comes to roll forming metals, pre-finished and plain. Such as profiles, U-Channels, C-Channels, J-Channels, Hat Channels, Box Channels, Zee Channels, Strut Channels, moldings, and more.
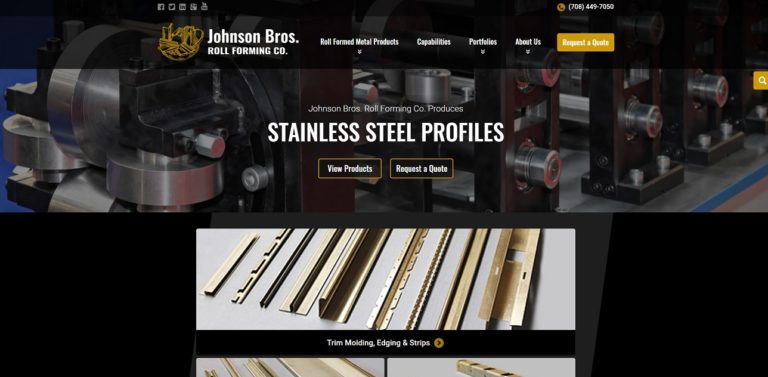
With over 50 years of experience, United Roll Forming specializes in roll forming for a variety of industries. Our products are the result of state-of-the-art machines that provide both quality and efficiency.
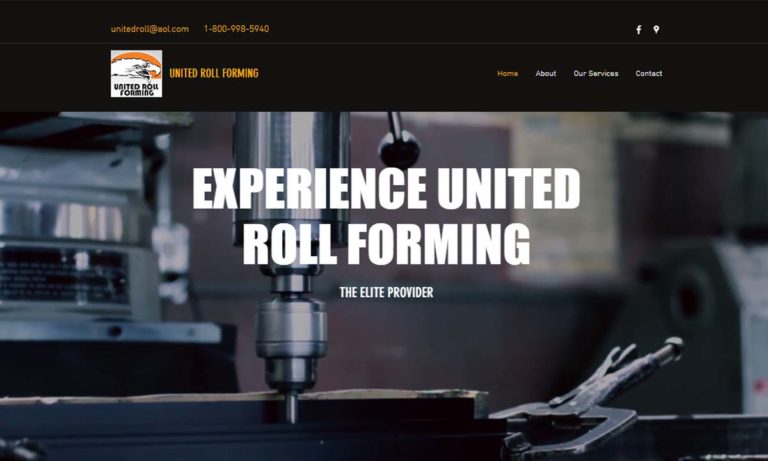
Producing five different standard products, as well as complicated roll forming sections and secondary operations such as notching, punching and fabricating, is Roller Die & Forming Company, Inc. They provide in-house tool room for quality metal moldings and the employees have been trained in every aspect of the roll forming process, representing over 200 years of experience.
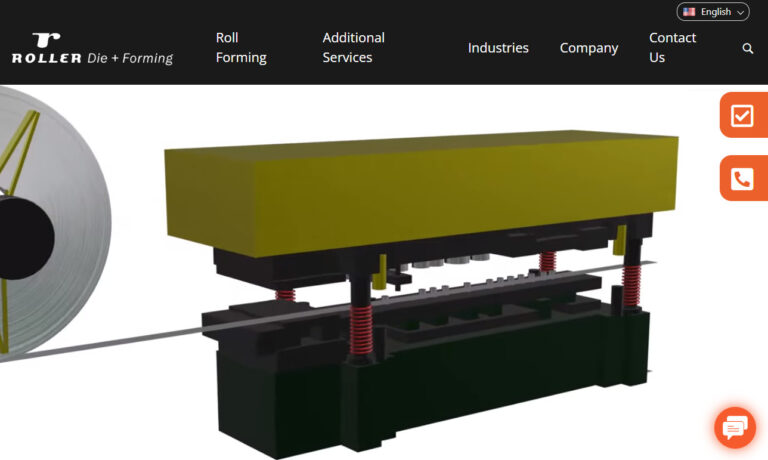
Premier Products of Racine is a full-service company established in 1999 that provides custom roll formed products for applications such as outdoor appliances, tanker trucks, and office furniture. Our 40,000-square-foot facility enables us to perform a variety of additional processes such as custom packaging, welding, and riveting. For more information on what we can do for you, call or visit our ...
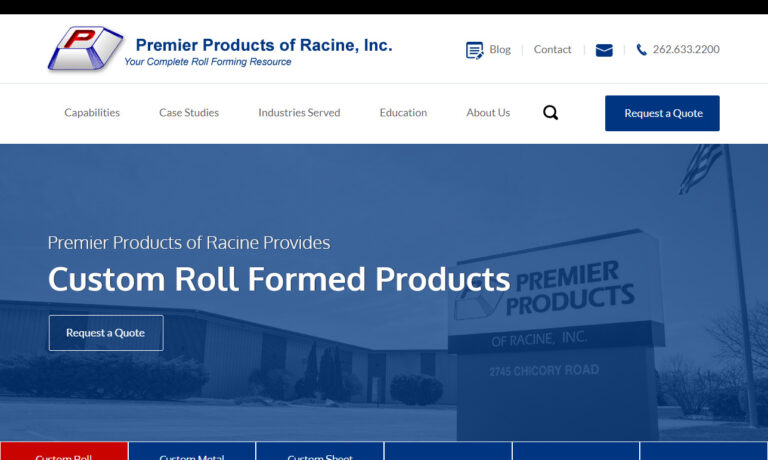
At MMC Roll Form, we specialize in delivering precision-engineered roll formed parts tailored to meet the unique requirements of every project. With over five decades of experience, we’ve built a reputation as trusted partners in the roll forming industry by combining technical expertise with a commitment to personalized service.

More Roll Forming Companies
Products Produced
Roll forming is a highly versatile metalworking process employed across a vast range of industries, enabling the efficient mass production of custom metal profiles and standardized shapes. Common products created through roll forming include angle irons, aluminum and steel angles, metal channels, trims, wall panels, and circular metal rings. Additionally, roll formed items can be tailored for specific uses, such as seat tracks in buses. The flexibility, speed, and cost efficiency of roll forming make it an ideal choice for manufacturing both simple and intricate metal components.
In the realms of carpentry and construction, roll formed angles are crafted to fortify structures bidirectionally, often equipped with slots or apertures to facilitate connections. In a similar vein, metal channels in these fields offer foundational support to rails and frames, extending their utility to the fabrication of goods across consumer, industrial, and commercial sectors. Metal trim, meanwhile, neatly outlines the contours of parts or products—providing both structural support and aesthetic refinement. In industrial and commercial settings, roll formed metal wall panels shield factory interiors from sparks and debris or aesthetically transform the facades of office buildings. Metal rings, those simple loops of metal, fulfill diverse roles—from encasing elevator buttons and enhancing telephone interfaces to decorating apparel, anchoring street signs, securing door locks, and maintaining hose connections.
Other widely manufactured roll formed components include steel purlins, guard rails, metal studs, framing members, stair stringers, and even custom enclosures or housings for electronics and machinery. The automotive, aerospace, HVAC, agricultural, and energy industries frequently rely on roll formed profiles for applications such as reinforcement beams, window frames, solar panel mounts, and more.
History
The origins of rolling technology stretch back to around 600 B.C., with the earliest prototypes of rolling mills unearthed in South Asia and the Middle East. These ancient machines, operating on fundamental principles later illustrated by Da Vinci during the Italian Renaissance, mark the inception of this enduring technology.
Though Da Vinci originally conceptualized rolling machinery, it wasn’t produced during his lifetime. The first actual rolling former, the slitting mill, was introduced in England around 1590, 70 years after his death. In this process, workers inserted flat iron bars into the mill, where they were first shaped into plates and then slit into strips using grooved rolls. Over time, engineers made modifications to the slitting mill, enabling it to also produce roll hoops for barrels.
In the waning years of the 17th century, curious minds turned their attention to the art of rolling tin. In 1697, a British visionary, Major John Hanbury, established a pioneering mill dedicated to shaping “blackplate”—a term for uncoated iron or steel that has undergone annealing. As his ambitions evolved, Hanbury shifted his focus to “tinplate,” a sleek, tin-coated steel. The wave of innovation continued, and in 1759, Thomas Blockley, another British innovator, secured a patent for his method of polishing and rolling metals. A few years later, in 1766, Richard Ford broke new ground with his patent for the world’s first official tandem mill. These tandem mills, designed to roll metal through successive stands, became instrumental in producing hot roll wire rods.
The art of roll forming as it is practiced today traces its origins back to the inventive mind of Henry Cort in the late 18th century. In 1783, Cort secured a patent for a revolutionary method of rolling iron bars using grooved rolls. Although he wasn’t the pioneer of using grooved rolls, his genius lay in integrating this technique with other processes in a novel way. His innovative design dramatically increased productivity, enabling mill workers to produce fifteen times more output per day than previously possible. Thanks to his groundbreaking contributions, Henry Cort is celebrated as the “father of modern rolling.” Cort’s innovation was a pivotal moment in the evolution of roll forming. Following his breakthrough, a wave of engineers and manufacturers emerged, each tweaking and expanding the process to suit their specific needs and the emerging technologies of their times. As technological advancements surged, so did the size of rolling mills and the scale of the products they churned out. A striking example was seen at The Great Exhibition of 1851, where the Consett Iron Company displayed their prowess by showcasing an enormous steel plate that tipped the scales at 1,125 pounds, stretched 20 feet in length, was 3 ½ feet across, and boasted a thickness of 7/16 inches. Merely two years later, the industry made another leap forward as manufacturers started rolling heavy sections with the introduction of “three high” mills.
The landmark strides of the 20th and 21st centuries have largely been driven by the sweeping tide of automation. In the present day, manufacturers of roll formed parts harness the power of CNC technology to meticulously craft their designs digitally before employing the same sophisticated systems to bring them to life. Thanks to this integration of technology, modern roll forming achieves unparalleled precision, complexity, and consistency, propelling the rolling and bending machine market to thriving new heights. Today, automated roll forming lines are capable of mass-producing custom profiles with tight tolerances, supporting the evolving needs of industries ranging from construction and infrastructure to renewable energy and transportation.
Materials Process
A key advantage of roll forming is its adaptability to a broad spectrum of metals and alloys. Many metals, whether they contain iron (ferrous) or not (non-ferrous), are suitable for roll forming. Brass, steel, zinc, aluminum, zirconium, titanium, and tin are some of the most frequently shaped metals using this process. The choice of material is guided by the intended application, required strength, corrosion resistance, finish, and cost constraints.
Brass
Brass, a lustrous alloy primarily composed of copper and zinc, is celebrated for its radiant, golden sheen. The myriad forms of brass each display unique measures of its quintessential traits: durability, pliability, luster, resistance to corrosion, and antimicrobial properties. Roll formed brass profiles are commonly used in architectural trim, decorative moldings, connectors, and electronic components due to their conductivity and aesthetic appeal.
Steel
Steel reigns as a favorite in the realm of roll forming, cherished for its robust and enduring qualities. It boasts an impressive portfolio: strength that withstands the rigors of use, durability for the long haul, hypoallergenic properties for sensitive applications, resistance to abrasion, and a defiance against corrosion. To meet the diverse demands of its myriad applications, artisans blend an array of steel types and grades, including stainless steel, carbon steel, and galvanized steel, each tailored to specific needs. Steel roll formed products include structural beams, wall studs, electrical enclosures, and construction panels.
Zinc
Zinc, a naturally-occurring element, seldom stands alone in nature. This lustrous, bluish-white metal may appear delicate and brittle, yet it possesses moderate conductivity. To harness its potential, manufacturers often blend it with other elements, crafting sturdy and valuable alloys such as brass and bronze. Roll formed zinc components are valued in the building industry for roofing, guttering, and architectural details due to their corrosion resistance.
Aluminum
Aluminum, a timeless and nonferrous metal, has gracefully woven its story through the centuries, first making its mark as early as the fifth century. Celebrated for its symphony of traits—it conducts electricity with ease, warms and cools with swift precision, molds to the wildest imaginations, stretches without snapping, resists the ravages of rust and flames, repels magnetic advances, and mirrors light with a gleam—it’s no wonder this metal has consistently been a material of choice through the ages. Aluminum roll formed parts are found in window frames, curtain wall systems, transportation, and solar panel mounting systems.
Zirconium
Zirconium metal is sourced from the mineral zircon. Known for its impressive resistance to corrosion, it finds its place in specialized uses including light filaments, surgical instruments, and as protective cladding in nuclear reactors. Roll forming allows zirconium to be shaped into precise components for the nuclear and medical industries.
Titanium
Manufacturers often choose titanium when they need to craft parts for heavy-duty applications. This metal stands out for its remarkable strength-to-weight ratio and has a high melting point, impressive ductility, and low density. Additionally, titanium is resistant to both freshwater and saltwater corrosion, withstands high temperatures, and is resilient against fatigue and cracking. Roll formed titanium is used in aerospace, defense, and high-performance automotive applications.
Tin
Tin, a metal frequently mingled in alloys, has partnered with elements like copper for millennia to forge materials of significant utility. In its natural state, tin boasts a soft, pliable nature, resists corrosion from water, and takes on a shine with ease. When combined with other metals, tin’s resilience against both acid and alkali corrosion is notably enhanced. Roll formed tin is commonly used in food packaging, electronics, and specialty industrial applications.
Looking for guidance on choosing the right material for your roll formed product? Consider the end use, environment, load-bearing requirements, and aesthetic preferences. Reach out to trusted roll forming companies for expert recommendations tailored to your project.
Process Details
Roll forming transforms the character of metal without the fiery touch of heat. Instead, it employs the relentless embrace of force and compression. As the metal passes through a series of rollers, each exertion crafts it further, instilling the final product with inherent strength and enduring resilience. To understand this transformation, let’s walk through the roll forming process step by step.
Step 1
Before proceeding with any other steps, roll form service providers must carefully select their materials, typically opting for metal strip coils. This choice is strategic: coils are not only readily available but also exceptionally convenient for feeding into the machinery. Material selection is based on desired mechanical properties, surface finish, and dimensional tolerances.
Step 2
The metal, whether stock or custom-shaped, is introduced to an initial set of roller dies crafted to closely embrace its contours. These dies might be positioned horizontally, or they might rotate or roll. Typically, the metal is fed into the machine at room temperature, a process referred to as cold roll forming. This cold working process improves the metal’s mechanical properties, such as yield strength and hardness, without the need for heating.
Step 3
The roll form machine steadily guides the metal through a sequence of rollers, each meticulously positioned a bit differently from the last. This progressive arrangement subtly molds the metal, step by step, into its newly rolled shape. The number of passes and the design of each roller station are determined by the complexity of the final profile and the thickness of the material.
Step 4
The subsequent phase, trimming to specifications, is not always necessary. Typically, manufacturers work with endless rolls of metal that are sized down post-roll, a process known as post-cut rolling. This method stands out for its efficiency and uniformity. On the other hand, there are times when manufacturers opt to slice the metal before it enters the rolling phase (pre-cut rolling), allowing them to bypass this step altogether. Secondary operations—including punching, embossing, or notching—can be integrated inline or performed as post-processing steps to add features or holes to the final product.
Curious how roll forming compares to other metalworking processes? Explore process variations and alternatives below to find the best fit for your manufacturing needs.
Design
Manufacturers regularly produce both standard and bespoke roll-formed products. In sculpting each metal shape, they meticulously evaluate factors such as bend radius, diameter, size, sheet metal thickness, and the material properties of the metal. Roll forming is a flexible, modular process, allowing the machinery to be adapted and re-adapted to craft a diverse array of metal configurations. Additionally, by integrating punching equipment and various other components, roll forming machines unlock a vast array of possibilities. However, their capabilities do have bounds, particularly in creating sealed ring products. Such items necessitate secondary processing, as these machines cannot fabricate closed loops on their own. Instead, ring products need to be either welded or joined with fasteners to achieve a sealed state.
Interested in custom roll formed profiles or unique metal shapes? Many roll forming companies offer in-house engineering support to help you optimize your product design for manufacturability, cost, and performance. Whether you need complex cross-sections, tight tolerances, or high-strength alloys, roll forming can often deliver superior results compared to traditional extrusion or stamping.
Machinery Used
Rolling Machine
The fundamental rolling machine features a series of distinct stations: an entry point where metal is inserted, a roller station tasked with shaping the metal, a cut-off press designed to slice the metal to precise lengths, and an exit section where the finished product emerges.
Many rolling machines are equipped with additional elements and roll form tooling to enhance their versatility. Examples of these enhancements include TIG welding technology, lasers, press brakes, punching tools, and bending tools. Modern roll forming lines often feature automated controls, quick-change tooling, and integrated quality inspection systems to ensure maximum efficiency, accuracy, and repeatability.
What types of roll forming machines are best suited for your project? Choices range from single-stand machines for basic profiles to multi-stand, CNC-controlled lines for complex, custom shapes and high-speed production.
Variations and Similar Processes
Hydroform Press Forming
Hydroform press forming, commonly known as hydroforming, is a technique where room temperature materials are shaped using high-pressure hydraulic fluid. Within the mold, the metal conforms to its designated shape. When used with ductile metals, hydroforming presents a cost-effective method to produce lightweight, durable, and structurally robust parts and products. This process is predominantly employed in the automotive industry.
Other related processes include press braking, stamping, extrusion, and draw forming. Each method offers unique advantages—press braking excels at short-run, large-bend parts; extrusion is often used for continuous, solid or hollow profiles; stamping is ideal for high-volume production of flat parts with complex features. Understanding the strengths and limitations of each process will help you select the best method for your specific application.
Benefits
Roll form parts are prized for numerous reasons, including their consistency, precision, and robust construction. This process also brings the advantages of being cost-effective, versatile, and producing long-lasting results. Let’s explore the key benefits of roll forming in greater detail:
Cost-Effectiveness
To begin with, roll forming is exceptionally cost-effective and profitable due to its minimal scrap production and low energy consumption. The process boasts low tooling costs and utilizes nearly 94% of the material fed into the machinery. Additionally, the continuous production capability of roll forming enables the efficient completion of high-volume orders, further enhancing its cost-effectiveness. For those seeking to reduce manufacturing costs without sacrificing quality, roll forming offers a compelling solution for both OEMs and custom fabricators.
Versatility
Furthermore, the potential applications for roll-formed parts are vast and seemingly limitless. Rollers can be treated with non-reactive powders or oils, ensuring that the surface properties remain unaffected. This allows roll-formed parts to undergo coating, polishing, finishing, curing, and other treatments effectively. Additionally, due to its modular nature, the roll forming process can be continuously reconfigured, allowing for customized roll forming to meet specific needs. From intricate profiles for electronics to heavy-duty structural beams, roll forming is adaptable for diverse sectors.
Durability by Compressive Stress
Ultimately, regardless of the specific characteristics of a roll-formed part, both manufacturers and customers can trust that the compressive stress used in its creation ensures it will be robust and long-lasting. The gradual shaping process enhances the mechanical properties of the metal, resulting in components that are strong, stable, and resistant to deformation under load.
Additional advantages of roll forming include fast lead times, minimal secondary processing, high repeatability, and suitability for both prototype and production runs. As a result, roll forming is a preferred manufacturing method for clients demanding high quality, tight tolerances, and scalability.
Applications and Industries Served
Roll forming is a cornerstone process for many critical industries. Construction and building companies rely on roll formed steel studs, channels, and trims for framing and architectural features. In the automotive industry, roll forming produces structural rails, bumpers, seat tracks, and window guides. The HVAC sector uses roll formed ducts, housings, and brackets for efficient airflow and installation. Electrical enclosures, solar panel frames, shelving, racking systems, street sign brackets, and fencing are just some examples of the broad application landscape of roll formed products.
Need help identifying the right roll formed product for your industry or project? Browse our company listings or contact us for expert guidance on roll forming applications, materials, and design options.
Decision Factors: How to Choose a Roll Forming Partner
To secure the finest quality product at a fair price, partnering with an experienced and reputable manufacturing company is essential. To aid you in your quest, we’ve curated a list of top-notch roll formed part suppliers and manufacturers. While all on our list uphold high standards, not every one will perfectly suit your specific needs. The ideal match for you will be the one that aligns best with your requirements.
- Capabilities & Equipment: Does the company offer advanced CNC roll forming, custom tooling, and integrated secondary operations such as punching or welding?
- Materials Expertise: Can the supplier process your required metal—be it steel, aluminum, brass, titanium, or specialty alloys?
- Quality Assurance: What ISO certifications, inspection protocols, and quality guarantees are in place?
- Lead Time & Flexibility: What are the typical turnaround times, and can the company accommodate urgent orders or design changes?
- Experience & Industry Knowledge: Does the partner have proven experience in your application area—such as automotive, construction, or renewable energy?
- Customer Service & Support: Are quoting, design consultations, and after-sales service responsive and professional?
So, how do you find the perfect fit? Begin by exploring the companies listed in our directory, examining their profiles and visiting their linked websites. Immerse yourself in what each has to offer. For insights into their customer service, refer to resources like company reviews and client testimonials. As you gather information, identify three or four companies that stand out to you. Reach out to them to discuss your specific needs, including turnaround times, customization options, delivery methods, and standard certifications. Request a quote from each and compare not only the prices but also the quality of your interactions. Select the company that you feel best meets your needs, then contact them again to commence your partnership.
Ready to request a quote for roll formed parts? Visit our Roll Forming Companies directory to connect with leading suppliers.
Frequently Asked Questions About Roll Forming
- What is roll forming and how is it different from stamping?
Roll forming is a continuous metal forming process that creates long profiles with consistent cross sections, ideal for high-volume production of complex shapes. Stamping, by contrast, is better suited for flat or shallow parts produced in discrete steps. - What materials can be roll formed?
Most ductile metals—including steel, aluminum, brass, copper, zinc, and titanium—can be roll formed, provided the material thickness is compatible with the machine’s capacity. - How do I design a part for roll forming?
Work with your roll forming supplier early in the process to optimize the profile for manufacturability. Factors such as minimum bend radii, material selection, and required tolerances should be considered. - What are typical tolerances for roll formed parts?
Tolerances depend on material, part geometry, and equipment, but modern CNC roll forming lines can achieve dimensional tolerances as tight as ±0.010″ (0.25mm) or better for many profiles. - Is roll forming cost-effective for small batch production?
While roll forming excels at high-volume runs due to tooling costs, quick tool changes and modular setups now make it viable for small and medium batches, especially for complex or custom profiles.
Still have questions? Contact us or browse our directory to find roll forming experts ready to assist with your specific application.
Explore More Resources
For additional information on related metalworking processes, materials, and suppliers, explore our partner sites:
- Check out our Wire Rope website
- Check out our Forgings website
Whether you’re comparing roll forming to extrusion, seeking the best supplier for metal channel production, or simply researching the latest advances in metal fabrication, our comprehensive resources are designed to support your buying decisions and technical questions.
Ready to take the next step? Browse roll forming companies now or ask us a question for personalized assistance.